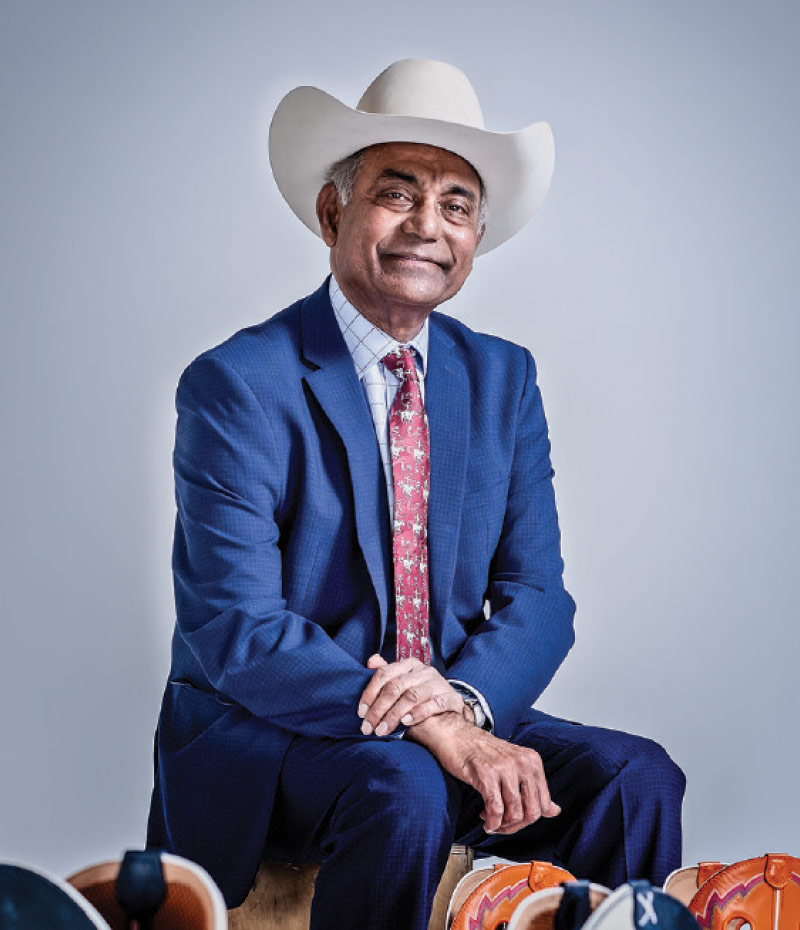
Most sustainability experts consider circularity the holy grail of manufacturing. In simple terms, it means producing zero waste. That is what Twisted X Global Brands (Twisted X, Wrangler, and Black Star) hopes to work toward, beginning this fall—once its state-of-the-art grinders get fully up and running at partner factories in the Americas and, this January, at its Decatur, TX, headquarters.
CEO Prasad Reddy can’t wait to start throwing mounds of PU, EVA, rubber, end-of-life footwear, and (potentially) textile waste into the grinders and turning that trash into shoes. “This is a totally new play for us where we are removing waste from landfills in a different way than we’ve done before,” he says. “For example, with Zero-X we removed harmful glues from the process, but here we are truly going to remove factory waste. This is full circle because we are not contributing to factory waste; we are grinding and upcycling into other industries and offerings.”
The yet-to-be-named program could be used across the company’s brand portfolio, primarily in casual styles. “What we’ve tested so far doesn’t compromise on comfort, and the durability is good, but it isn’t quite as durable as a rubber sole used for work wear,” Reddy says. “So, the material will lean more toward use in casual comfort styles at the start.”
As for how much waste Twisted X hopes to redirect from landfills, Reddy says the more the merrier. “At this moment we don’t have an estimate, but we feel the impact is going to be huge,” he says, noting it depends on how many pairs are sold. That aside, the grinding process bodes well on how much waste can be repurposed as it essentially squishes it down to approximately 1/20th of the original volume. “The first round of our process is expected to save 90 percent in volume of waste going into landfills. Then it can be reground even further,” he says. “The first round can be used in variety of footwear profiles, while grinds from round two can be used in flip-flops only, and round three grinds can be used by other companies for products like doormats, gym mats, and cushioning filler in sofas and automotive seats.”
The ability to keep regrinding and repurposing waste is what has Reddy most excited about the program’s long-term potential. “It’s not single use. This is a full circular initiative,” he says. “The next level up will be using the grindings for the entire shoe. So, zero waste is where we’re headed.”